Enhancing Manufacturing Operations with AI and IoT Solutions
The manufacturing industry is rapidly evolving with the integration of AI and IoT technologies, driving improvements in quality control, asset management, workplace safety, and data-driven decision-making. These advanced solutions help manufacturers enhance efficiency, reduce downtime, and ensure a safer working environment. Below is an overview of the transformative potential of AI and IoT solutions across various aspects of manufacturing.
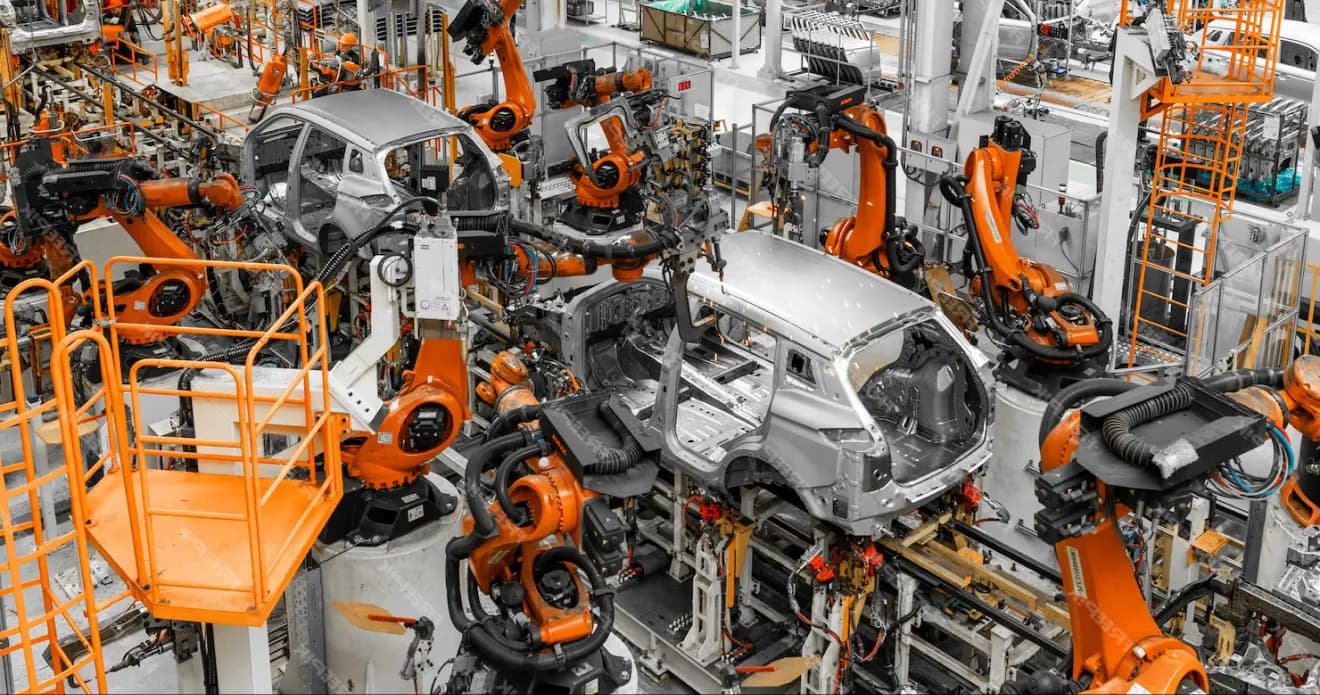
AI Visual Inspection
In manufacturing, quality and precision are non-negotiable, yet manual inspection often struggles to keep up with the growing demand for consistency and speed. Integrating AI Visual Inspection systems directly onto production lines or attaching them to Cobots is helping manufacturers detect defects early, minimize waste, and ensure top-notch product quality. Powered by Computer Vision AI and AI defect detection, these solutions bring a new level of accuracy, reducing human fatigue and errors. This shift is not just about automation-it’s about creating safer, more efficient factories where humans and machines work together for AI Quality Control excellence.
Surface Defect Detection
Surface Defect Detection on Metal and Plastic Components
Offshore drilling operations rely on heavy machinery that must function seamlessly in harsh environments. Unexpected equipment failures lead to costly downtime and safety hazards. AI development agencies are addressing these challenges by providing AI-based software development for predictive maintenance, allowing companies to stay ahead of failures and optimize performance.
Challenges
• Tiny cracks, scratches, or dents are difficult for the human eye to detect consistently
• Manual inspection slows down production speed and impacts delivery timelines
• Human fatigue leads to inconsistent inspection results, especially during long shifts

Solution
AI Visual Inspection systems equipped with Computer Vision AI and AI defect detection algorithms scan metal and plastic parts in real-time directly on the production line or through Cobots. The system instantly flags any surface-level defects like scratches, dents, or discoloration for further review or automatic rejection.

Benefits
• Increases accuracy and consistency in detecting micro-level defects
• Reduces rework and production delays
• Minimizes human error and inspector fatigue
• Enhances product quality and customer satisfaction
• Allows seamless integration with Cobots for flexible deployment

AI-Based Leak Detection
Surface Defect Detection in Fabric Weaving and Knitting
Surface defects like yarn breakage, missing threads, or weaving faults are common in fabric production and often missed by manual inspection.
Challenges
• High-speed fabric production makes it difficult for human eyes to catch small defects
• Manual inspection is labor-intensive and inconsistent, especially in large-scale operations
• Delayed defect detection leads to significant material wastage

AI Solution
AI Visual Inspection systems with AI defect detection are deployed on looms or integrated with Cobots to scan fabrics in real-time. The system instantly identifies surface defects such as holes, floats, and misweaves, allowing immediate action to minimize losses.

Business Benefit
• Consistent and accurate detection of fabric defects
• Reduces fabric wastage and production downtime
• Improves overall product quality and customer satisfaction
• Enables faster production without compromising quality
• Minimizes dependency on manual inspection efforts

Packaging Inspection
Label, Barcode, and Packaging Inspection
The oil and gas industry involves high-risk environments where worker safety is a critical concern. Ensuring compliance with safety regulations and minimizing accidents is a challenge. AI software developers are providing AI-based software development solutions that enhance real-time workforce monitoring and improve safety protocols.
Challenges:
• Misaligned labels, incorrect barcodes, or damaged packaging impact brand image and logistics
• Incorrect packaging can lead to product rejection, delivery delays, or regulatory issues
• Human inspectors often miss subtle label or print defects in high-speed lines

Solution
AI Visual Inspection systems integrated with Cobots automatically verify label placement, barcode accuracy, and packaging integrity. Using Computer Vision AI, the system detects defects or mismatches instantly, allowing the line to correct or reject faulty items before shipment.

Benefits
• Improves packaging accuracy and compliance with shipping regulations
• Protects brand reputation by ensuring perfect packaging presentation
• Minimizes returns and logistical errors due to mislabeling
• Reduces manual labor, freeing up workers for higher-value tasks
• Enhances traceability and record-keeping for audits

AI and IoT Asset Performance Management
In today’s fast-paced manufacturing world, every machine, every minute, and every resource counts. Unexpected equipment failures or inefficiencies can bring production lines to a halt, leading to huge losses and delayed deliveries. That’s why manufacturers are turning to AI and IoT-driven Asset Performance Management (APM) solutions to gain real-time visibility, predict issues before they arise, and even prescribe the best corrective actions. Powered by Agentic AI, these technologies help factories move toward Industry 4.0 standards - enhancing productivity, sustainability, and machine life.
Predictive Maintenance
Predictive Maintenance of Critical Production Equipment
Manufacturing heavily depends on machineries like CNC machines, moulding units, and presses, where sudden failures can stop production and create costly bottlenecks.
Challenges
• Unpredictable equipment breakdowns causing costly unplanned downtime
• Over-reliance on scheduled maintenance, leading to unnecessary servicing or missed failures
• Poor visibility of asset health increases the risk of production loss

Solution
By integrating AI and IoT Asset Performance Management software with sensors and real-time data collection, manufacturers can monitor asset health, detect anomalies, and predict failures. Predictive maintenance powered by performance analytics ensures maintenance is performed only when needed, improving machine utilization and reducing downtime.

Benefits
• Reduces unplanned downtime and maintenance costs
• Extends machine life through targeted maintenance
• Improves Overall Equipment Effectiveness (OEE)
• Optimizes resource utilization and lowers spare part inventory
• Increases production reliability and throughput

Energy Optimization
Energy Consumption Monitoring and Optimization for Sustainability
Energy-intensive equipment like furnaces, compressors, and chillers can significantly impact operational costs and sustainability goals if not monitored and optimized.
Challenges
• Rising energy costs due to inefficient equipment operations
• Lack of real-time visibility into energy usage patterns
• Difficulty in achieving environmental compliance and sustainability targets

Solution
IoT Asset Management systems combined with Prescriptive Analytics monitor energy consumption in real time and suggest corrective actions like load balancing or switching to efficient modes. Asset Performance Management software identifies underperforming assets and guides operations toward energy-efficient practices.

Benefits
• Reduces energy wastage and operational costs
• Supports environmental sustainability goals
• Real-time insights help meet compliance standards
• Improves asset health and life cycle
• Enhances overall factory efficiency

Process Optimization
Production Line Bottleneck Identification and Process Optimization
Identifying and eliminating bottlenecks in complex production lines is essential for smooth manufacturing and timely deliveries.
Challenges
• Lack of real-time data leads to unidentified slowdowns and delays
• Manual analysis of production data is time-consuming and inaccurate
• Suboptimal utilization of machines affects production targets

Solution
By deploying AI-driven Asset Performance Management software and real-time asset tracking, manufacturers can monitor each machine's performance across the production line. Predictive Analytics and Performance Analytics help spot bottlenecks and suggest process changes or reallocation of resources to maintain flow.

Benefits
• Increases production throughput by eliminating bottlenecks
• Enhances Overall Equipment Effectiveness (OEE)
• Enables data-driven decision-making for continuous improvement
• Reduces cycle times and operational costs
• Improves customer satisfaction with timely deliveries

AI Software Development
The manufacturing industry is evolving rapidly, where efficiency, precision, and customer satisfaction define success. In this journey, AI development companies and AI consultants are helping manufacturers reimagine operations, optimize production, reduce waste, and deliver better customer experiences. With the support of skilled AI software developers and custom-built AI solutions, manufacturers can turn complex data into actionable insights - driving smarter decisions and sustainable growth. Below are three popular use cases where AI is transforming the manufacturing sector.
AI-Powered Production Optimization and Waste Reduction
Production Process Optimization
In manufacturing, balancing maximum production output with minimum waste is a constant struggle. Every inefficient process or material overuse directly impacts profitability and contributes to environmental harm. Today, more manufacturers are turning to AI consultants and AI development companies to build smart production optimization tools. These AI software developers create solutions that monitor, analyze, and fine-tune production processes in real-time, helping companies operate smarter and greener.
Challenges
• Inconsistent Production Processes: Manual monitoring or outdated systems lead to variations in quality and excessive material waste, driving up costs.
• Lack of Real-Time Insights: Without data-driven intelligence, detecting inefficiencies and defects mid-production becomes impossible until it’s too late.
• High Operational Costs: Inefficient use of raw materials, energy, and labor increases production costs and lowers overall profitability.
• Environmental Impact: Excessive waste and energy consumption make it difficult for manufacturers to meet environmental sustainability goals.

Solution
Manufacturers are partnering with expert AI companies and AI software developers to build AI-powered production optimization platforms tailored to their operations. These systems use machine learning, computer vision AI, and real-time data to monitor production lines, detect inefficiencies, and suggest improvements instantly. By continuously analyzing data, they help reduce material waste, prevent defects, and improve overall efficiency. With guidance from AI consultants, manufacturers achieve smarter, more sustainable, and cost-effective production processes.

Benefits
• Reduced Material Waste: AI-driven adjustments minimize scrap, rework, and excess raw material use, saving costs and resources.
• Improved Production Efficiency: Identifies and resolves inefficiencies early, leading to higher yields and smoother operations.
• Real-Time Process Corrections: Automated monitoring allows instant corrections, reducing defects and ensuring quality output.
• Supports Sustainability Initiatives: Less waste and optimized resource use contribute to meeting environmental goals and reducing carbon footprint.
• Lower Operational Costs: By optimizing material use and improving energy efficiency, manufacturers significantly cut production costs.

AI-Driven Customer Demand Forecasting
AI-Driven Customer Demand Forecasting and Service Enhancement
In today’s highly competitive manufacturing landscape, understanding what customers want-and when they want it-is everything. Poor demand forecasting leads to stockouts, production chaos, and unhappy customers. That’s why forward-thinking manufacturers are partnering with expert AI consultants and AI development companies to develop AI-driven demand forecasting tools. These tools don’t just crunch numbers; they provide real-time insights that improve production planning, optimize inventory, and elevate customer service.
Challenges
• Inaccurate Sales Predictions: Traditional forecasting methods struggle to keep up with rapidly changing market trends, seasonal spikes, and unpredictable customer behavior. This results in frequent stockouts or costly overproduction.
• Poor Customer Service: Delayed deliveries or incorrect inventory levels lead to dissatisfied customers, damaged relationships, and loss of trust.
• Higher Holding Costs & Lost Revenue: Overstocking ties up working capital in unsold goods, while stockouts mean lost sales opportunities and unhappy customers.

Solution
Manufacturers are increasingly teaming up with AI software developers and AI companies to create smarter, AI-powered demand forecasting platforms tailored to their needs. These platforms tap into predictive analytics and machine learning to sift through vast datasets - from past sales and market trends to customer buying patterns and even factors like weather or economic shifts. The goal is simple: help businesses stay ahead of demand, avoid stockouts or overproduction, and serve their customers better. With the right AI consultants guiding the process, manufacturers gain the insights they need to plan smarter and operate more efficiently.

Key Features
• Real-time Demand Prediction: AI models forecast product demand more accurately than traditional methods, helping manufacturers prepare for market changes.
• Dynamic Production Planning: AI-driven systems adjust production schedules in real time based on updated demand forecasts and inventory levels.
• Customer Behavior Analysis: By learning from customer purchase patterns, AI tools help companies anticipate preferences and improve service delivery.
• Personalized AI Consulting: Skilled AI consultants tailor models for specific industries, product categories, and customer segments to maximize accuracy and impact.

Benefits
• Accurate Demand Forecasting: Reduces overproduction and prevents stockouts, leading to optimized inventory and lower holding costs.
• Improved Production Planning: Enhances resource allocation and manufacturing efficiency by aligning production with real-time demand signals.
• Superior Customer Satisfaction: Timely deliveries and better service strengthen customer relationships and loyalty.
• Increased Sales & Revenue: By meeting customer demand effectively, companies boost sales while minimizing waste.
• Stronger Market Position: AI-driven insights allow companies to stay agile and respond faster to changing market dynamics.

AI-Optimized Supply Chain Management
AI-Optimized Supply Chain Management
Managing the supply chain in manufacturing is complex and prone to disruptions. AI-optimized supply chain management leverages advanced AI technologies to enhance demand forecasting, inventory management, and logistics planning, ensuring efficiency and customer satisfaction.
Challenges
• Demand Forecasting Errors: Traditional methods often fail to account for market fluctuations, seasonal demand, and sudden disruptions, leading to stockouts or overstocking.
• Inefficient Logistics and Routing: Manual route planning results in delays, increased fuel costs, and missed delivery deadlines.
• Poor Customer Experience: Delivery delays or inconsistent order fulfillment damage customer satisfaction and loyalty.

Solution
By collaborating with skilled AI developers, manufacturers can implement AI-powered supply chain management platforms that integrate with existing ERP and inventory systems. These platforms use predictive analytics and real-time data to forecast demand, automate inventory management, and optimize logistics.

Key Features
• Advanced Demand Forecasting: AI models analyze historical sales data, market trends, weather patterns, and external variables to predict product demand accurately.
• Smart Inventory Management: Automated inventory reordering systems maintain optimal stock levels, reducing the risk of overstocking and stockouts.
• AI-Driven Route Optimization: AI algorithms calculate the most efficient delivery routes, cutting fuel costs, improving delivery speed, and minimizing carbon emissions.
• Performance Analytics: Real-time monitoring of supply chain performance helps businesses make data-driven decisions to adapt to market changes swiftly.

Benefits
• 30% Reduction in Inventory Costs: Precise demand forecasting avoids costly overstocking and reduces storage expenses.
• 15–25% Fuel and Logistics Savings: AI-optimized routes lead to faster deliveries and significant fuel cost reductions.
• Enhanced Customer Satisfaction: On-time deliveries improve customer loyalty and trust.
• Sustainability: Efficient resource use and reduced carbon emissions support corporate sustainability goals.
• Improved Decision-Making: Access to real-time performance data empowers managers to make proactive decisions.

AI People and Process monitoring
In today’s fast-moving manufacturing world, knowing exactly where your people are and how your processes run isn’t just important-it’s critical. AI-powered people tracking and process monitoring are turning factories into smart, data-driven environments where every task, movement, and operation is optimized for precision, safety, and maximum output. By collaborating with expert AI consultants and AI development companies, manufacturers are unlocking real-time visibility and control like never before. Below are three powerful use cases that show how AI software developers are helping industries achieve next-level efficiency, accuracy, and safety-because in manufacturing, every second and every move counts.
Process Monitoring
AI-Driven Process Monitoring and Efficiency Optimization
Maintaining consistent quality and process efficiency is a constant challenge in manufacturing. AI-driven process monitoring helps identify bottlenecks, inefficiencies, and deviations in real time.
Challenges
• Manual process monitoring is prone to human error
• Difficulty identifying bottlenecks impacting production targets
• Quality issues going unnoticed until post-production

Solution
AI development companies design AI-powered process monitoring systems that leverage computer vision and machine learning to track workflows, equipment status, and human actions. The system provides real-time insights, enabling managers to adjust operations instantly.

Benefits
• Boosts overall efficiency and production output
• Early detection of quality issues, reducing waste and rework
• Enables real-time decision-making and optimization
• Data-driven continuous improvement for long-term gains

Activity Monitoring
AI-Powered Activity Monitoring for Accuracy and Precision in Critical Processes
In precision-driven manufacturing environments, even minor human errors or process deviations can lead to costly defects or rework. AI-based activity monitoring ensures workers follow standard operating procedures (SOPs) accurately, improving quality and operational precision.
Challenges
• Inconsistent task execution impacting product quality
• Difficulty tracking worker posture, tool usage, and task accuracy in real-time
• Increased rework and quality control costs due to unnoticed process errors

Solution
Partnering with AI consultants and AI development companies, manufacturers deploy computer vision and AI-powered activity monitoring systems. These tools track human movements, posture, and task execution accuracy during critical production stages. AI software developers fine-tune the system to detect deviations from SOPs, offering real-time alerts and detailed process reports for corrective actions.

Benefits
• Ensures tasks are performed with high accuracy and precision
• Minimizes human errors and reduces defects and rework
• Enhances quality control by identifying deviations early
• Supports continuous training and process improvement through actionable insights

Contractor and Visitor Tracking
Contractor and Visitor Tracking with Facial Recognition
Monitoring contractors and visitors in large manufacturing facilities is essential for both safety and compliance. AI-enabled facial recognition ensures only authorized personnel access critical areas.
Challenges
• Manual tracking of contractors/visitors is inefficient and error-prone
• Unauthorized access to sensitive production areas
• Difficulty maintaining compliance records and logs

Solution
AI consultants and AI software developers deploy facial recognition and AI people tracking systems that automate access control, monitor contractor movements, and maintain digital logs. Integrated with existing ERP or safety systems, the solution enhances both security and operational oversight.

Benefits
• Automated access control and reduced manual monitoring
• Improved site security and reduced safety risks
• Accurate record-keeping for compliance audits
• Ensures accountability and contractor performance monitoring
