Understanding AI Visual Inspection
AI Visual Inspection is redefining quality control in manufacturing. With its ability to detect defects in real time and adapt to changing production needs, it far outperforms traditional manual inspections. Backed by computer vision and machine learning, AI ensures consistent quality, reduces waste, and scales effortlessly. Here are five key benefits of bringing this technology into your manufacturing process. This blog will explore the five key benefits of integrating visual inspection AI into your manufacturing workflow.
Challenges of Traditional Manufacturing Inspection
Traditional inspection methods have limitations, as they rely on human expertise but are prone to fatigue, subjectivity, and inconsistencies. These challenges can lead to defects going unnoticed, increasing the risk of recalls, customer dissatisfaction, and operational inefficiencies.
Limitations of Manual Inspection:
• Human fatigue
Sustained inspections reduce accuracy over time.
• Subjective judgment
Different inspectors may interpret defects inconsistently.
• Scalability issues
Difficult to meet high production demands efficiently.
• High costs
Increased labor expenses and rework due to missed defects.
• Slower inspection speed
Struggles to keep pace with modern automated production lines
How AI Visual Inspection Transforms Quality Control
AI visual inspection addresses these challenges by automating the inspection process, providing consistent, accurate, and scalable quality control. Powered by sophisticated algorithms and computer vision, these systems can detect even the smallest anomalies and defects that would be easily missed by the human eye. By integrating visual inspection in manufacturing with AI, businesses can achieve unprecedented levels of quality and efficiency.
Game-Changing Benefits of AI Visual Inspection in Manufacturing
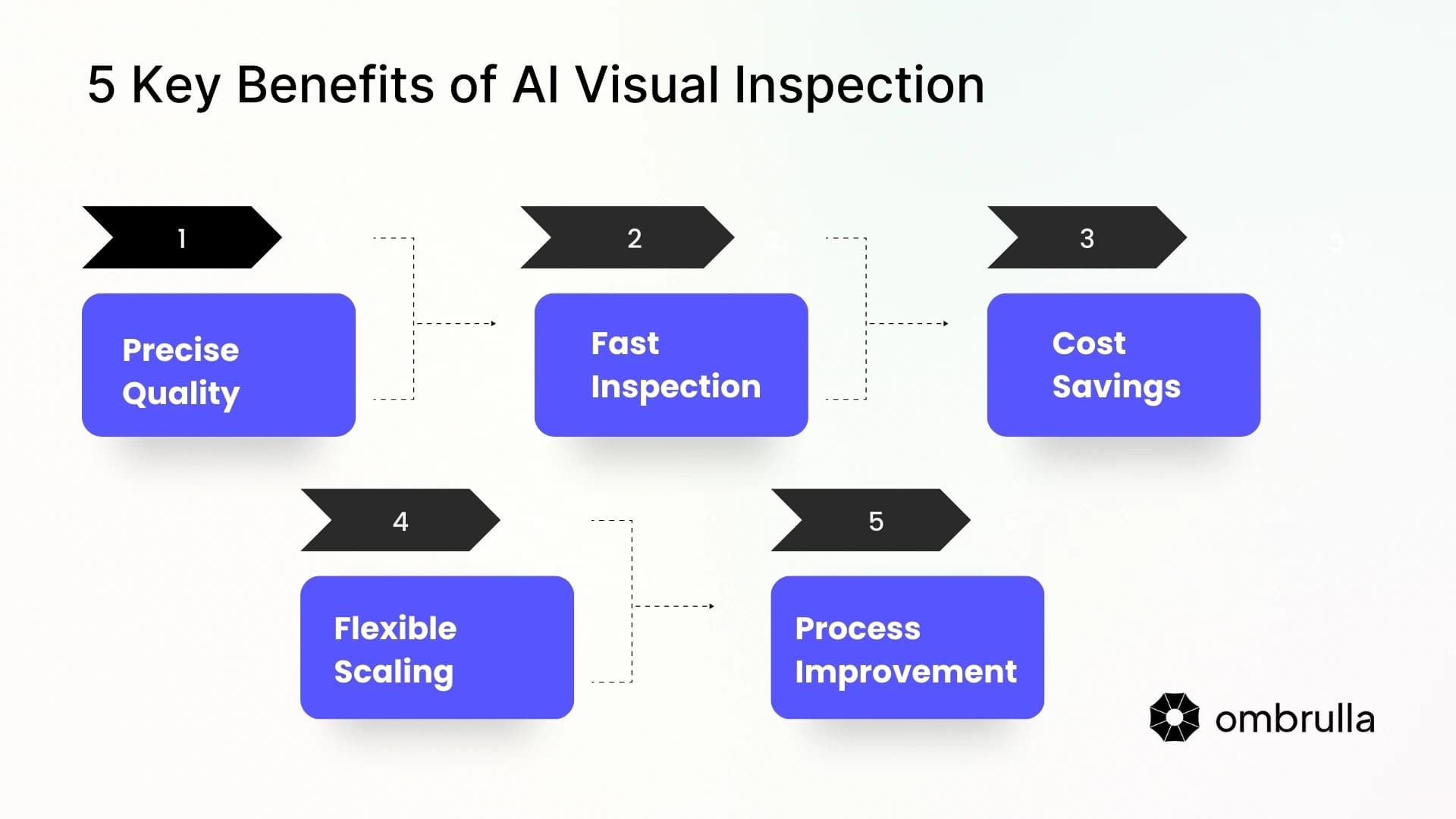
Here are five compelling reasons why your manufacturing operation needs AI defect detection and AI quality control:
1. Enhanced Accuracy and Consistency
2. Increased Speed and Throughput
3. Reduced Costs and Improved ROI
4. Improved Scalability and Adaptability
5. Data-Driven Insights and Process Optimization
Use Cases of AI Visual Inspection in Manufacturing
Here are some use cases of AI visual inspection across various manufacturing sectors
1. AI Visual Inspection in Automotive
• Paint Defect Detection
• AI systems identify scratches, dents, 'orange peel,' swirl marks, and other paint imperfections on car bodies, ensuring a flawless finish and reducing costly rework.• Component Assembly Verification
•AI checks the correct placement and alignment of parts on engine assembly lines, such as pistons, valves, and wiring harnesses, ensuring proper functionality and preventing engine failures.• Welding Quality Inspection
• AI analyzes weld seams for porosity, cracks, incomplete fusion, and other defects, ensuring structural integrity and safety in automotive components..• Tire Defect Detection
•AI identifies defects in tire treads, sidewalls, and beads, such as sidewall bulges, tread separation, and bead damage, preventing the production of unsafe tires and improving road safety..• Windshield Inspection
•AI detects scratches, cracks, delamination, and other imperfections in windshields, ensuring driver safety and visibility.
2. AI Visual Inspection in Electronics
• PCB Defect Detection
•AI identifies microscopic defects on printed circuit boards, such as solder bridges, missing components, incorrect component placement, and etching errors, leading to higher yields and reduced scrap.• Semiconductor Wafer Inspection:
• AI detects defects on semiconductor wafers, such as surface scratches, particle contamination, and circuit pattern errors, ensuring the quality of microchips and maximizing production efficiency.• Display Panel Inspection
•AI detects dead pixels, color inconsistencies, brightness variations, and other defects on display panels, ensuring high-quality displays for electronic devices.• Connector Inspection
• AI checks the alignment and integrity of electrical connectors, ensuring reliable connections and preventing electrical malfunctions in electronic devices.• Cable Harness Inspection
•AI verifies the correct wiring and connections in cable harnesses, preventing electrical malfunctions and ensuring the reliability of electronic systems.
3. AI Visual Inspection in Textiles
• Fabric Defect Detection
•AI identifies tears, stains, weaving imperfections, and other defects in fabric, allowing for early intervention and minimizing waste.• Garment Inspection
•AI checks the stitching, sizing, and overall quality of garments, ensuring consistent quality and reducing returns.• Leather Defect Detection
•AI identifies blemishes, scars, and other imperfections in leather hides, optimizing the use of materials and improving product quality.• Carpet Inspection
•AI detects defects in carpet pile, color, and backing, ensuring consistent quality and aesthetic appeal.• Yarn Quality Inspection
•AI checks the thickness, strength, and uniformity of yarn, improving the efficiency of textile manufacturing processes.
4. AI Visual Inspection in General Manufacturing
• Surface Defect Detection:
•AI identifies scratches, dents, corrosion, and other surface imperfections on metal, plastic, and other materials, ensuring product quality and preventing premature failure.• Dimensional Measurement
• AI measures the dimensions of parts and products to ensure they meet specifications, ensuring proper fit and function.• Assembly Verification:
•AI checks the correct assembly of complex products, such as machinery and appliances, ensuring proper functionality and preventing safety hazards.• Tool Wear Monitoring
•AI monitors the condition of cutting tools and other equipment, predicting when they need to be replaced, optimizing maintenance schedules and reducing downtime.• Safety Hazard Detection
•AI identifies potential safety hazards on the factory floor, such as spills, misplaced equipment, and obstructed walkways, improving worker safety and preventing accidents.
The adoption of AI visual inspection in the manufacturing industry is rapidly expanding due to its ability to improve quality, efficiency, and safety. Leveraging advancements in computer vision and deep learning, these systems can analyze images and videos with remarkable accuracy and speed. This technology is transforming how manufacturers approach quality control, moving from reactive to proactive strategies.
The Future of AI Visual Inspection in Manufacturing
Visual inspection in manufacturing is undergoing a rapid transformation, with AI at the forefront. As computer vision and machine learning technologies continue to advance, we can expect even more sophisticated and powerful AI-driven inspection systems in the future. These advancements will not only improve quality control but also pave the way for fully automated and intelligent manufacturing processes. The integration of AI into manufacturing inspection is not just a trend, it's a fundamental shift that's reshaping the industry.
Conclusion
In today's competitive manufacturing landscape, AI visual inspection overcomes traditional limitations, enhancing accuracy, speed, cost savings, and scalability. By adopting AI-driven quality control and defect detection, manufacturers can boost productivity, improve product quality, and gain a competitive edge. Investing in AI-powered inspection ensures not only better products but also a more efficient and future-ready manufacturing operation.




Related Blogs



