Overview: Reduce Downtime: Predictive Maintenance with AI and IoT
Predictive maintenance leverages the power of AI (Artificial Intelligence), IoT (Internet of Things), and APM (Asset Performance Management) to proactively identify potential equipment failures before they occur. IoT sensors continuously collect data from machines, which is then analyzed by AI models to detect anomalies, degradation patterns, and failure trends. With the introduction of Agentic AI, this process becomes even more intelligent-enabling autonomous decision-making, task scheduling, and real-time alerts without human intervention.
This AI and IoT-enabled predictive approach transforms maintenance from reactive to proactive, ensuring your assets remain efficient, reliable, and operational.
• Minimized Unplanned Downtime:
AI and Agentic AI work together to analyze asset data in real-time, predicting failures and allowing timely interventions before breakdowns disrupt operations.
• Optimized Maintenance Spend:
Predictive maintenance helps avoid unnecessary servicing, reduce spare parts inventory, and lower labor costs, enhancing overall APM strategies.
• Increased Asset Longevity & Efficiency:
Continuous monitoring through IoT and AI-driven insights ensures better asset health, improved productivity, and extended equipment life.
Benefits of Using APM Software for Predictive Maintenance
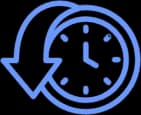
Zero Unplanned Downtime
Real-time monitoring through IoT sensors and AI analytics enables early detection of anomalies, helping prevent sudden equipment failures and ensuring continuous operations.
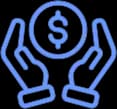
Autonomous Decision-Making with Agentic AI
Intelligent agents not only predict failures but also initiate corrective actions-like scheduling maintenance tasks or notifying the right teams-reducing human dependency and response time.
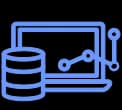
Lower Maintenance and Operational Costs
By servicing equipment only when needed, customers can avoid unnecessary repairs, reduce labor costs, and optimize spare parts inventory-leading to significant cost savings.

Improved Asset Health and Lifecycle
Continuous data analysis and automated interventions keep equipment running in optimal condition, extending the lifespan of assets and increasing their return on investment.
Transform Your Maintenance Strategy: Integrate Agentic AI for Unprecedented Foresight.
At Ombrulla, we empower industries to move from reactive and time-based maintenance to a proactive, intelligent, and autonomous approach using a powerful combination of AI, IoT, and Agentic AI. Our predictive maintenance platform is designed to continuously monitor asset health, forecast potential failures, and take timely action-minimizing risks and maximizing uptime.
IoT Integration
We connect your machines, sensors, and control systems through a unified IoT infrastructure - enabling real-time data collection across vibration, temperature, pressure, and other critical parameters.
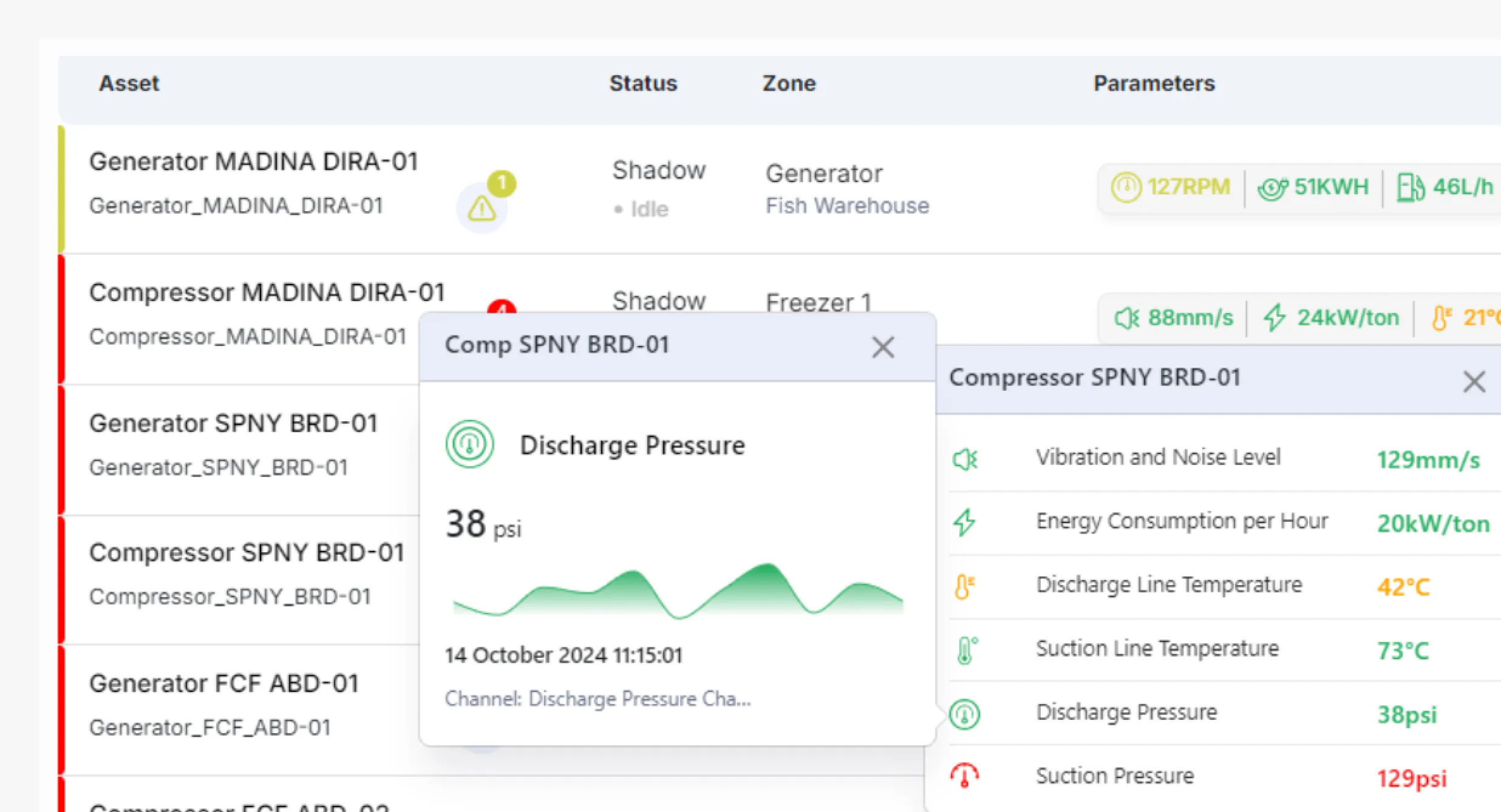
AI Analytics Engine
- Our AI models analyze historical and real-time data to detect patterns, anomalies, and degradation trends, providing early warnings before failures occur.

Agentic AI
- Unlike traditional systems, Ombrulla uses Agentic AI to enable self-governing agents that can initiate alerts, create maintenance schedules, and even trigger automated workflows-reducing human intervention.
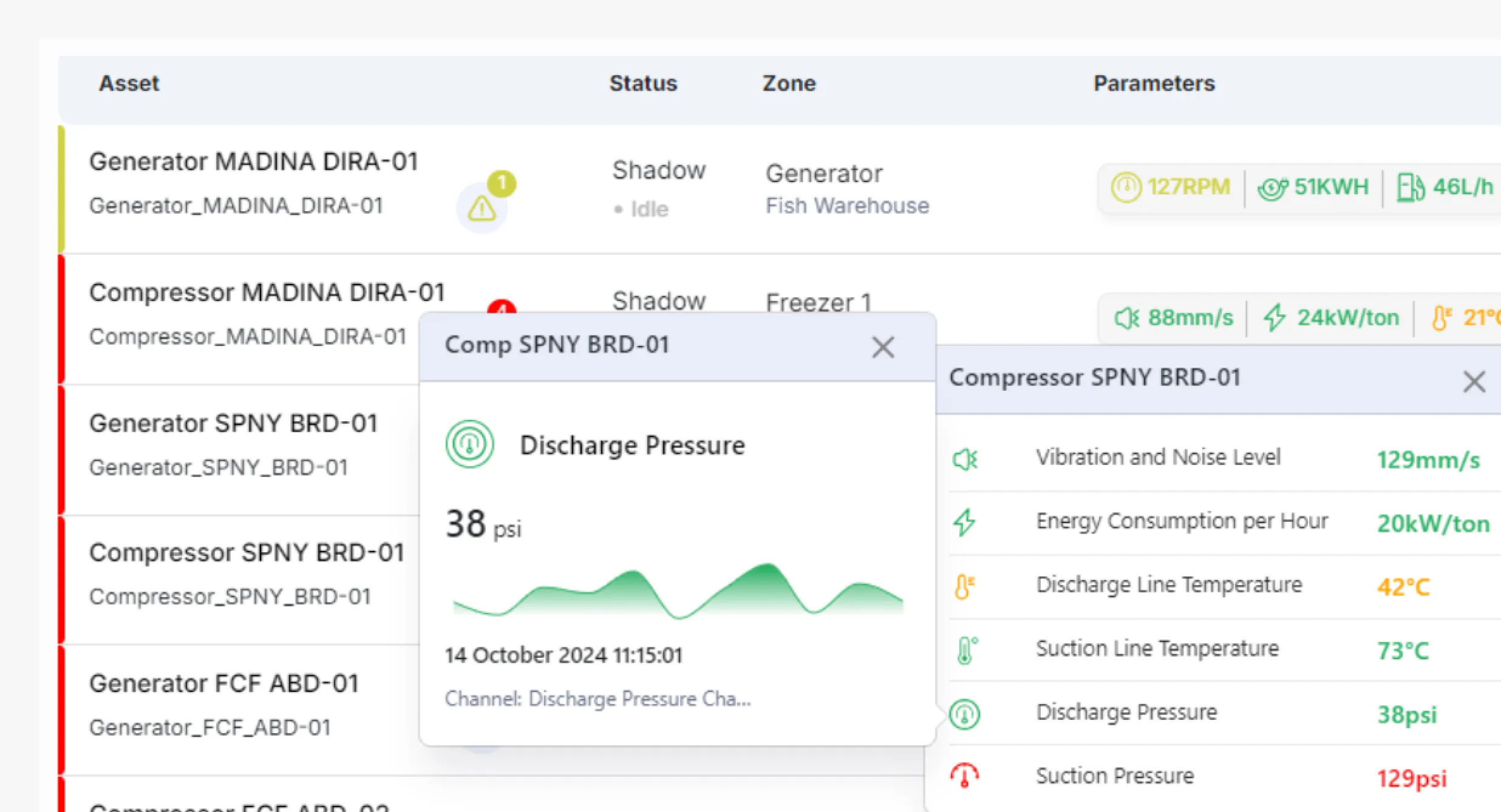
APM Dashboards
- Visualize the health, performance, and risk levels of all your critical assets through intuitive dashboards, with actionable insights tailored to your industry and asset types.

Integrate Agentic AI with Your Digital Twin: Achieve Intelligent Automation and Optimisation.
Implementing a successful Predictive Maintenance system with AI, IoT, and Agentic AI involves a structured, phased approach that ensures seamless integration, accurate predictions, and measurable outcomes. At Ombrulla, we follow a strategic process tailored to your industrial needs and asset types.
Step-by-Step Implementation Process
1. Assessment & Requirement Gathering
Analyze current maintenance workflows, identify critical assets, and define key performance indicators (KPIs). Understand the op
2. Sensor & IoT Infrastructure Setup
Deploy IoT-enabled sensors to collect real-time data on key parameters like vibration, temperature, humidity, pressure, and runtime. Establish secure data pipelines for continuous monitoring.
3. Data Integration & Preprocessing
Aggregate historical maintenance data, sensor feeds, and operational logs. Cleanse, normalize, and label data to ensure high-quality inputs for AI model training.
4. AI & Agentic AI Model Development
Train AI models to detect anomalies, predict failures, and generate insights. Integrate Agentic AI to automate decision-making processes such as maintenance alerts and task scheduling.
5. Platform Configuration & APM Dashboard Setup
Configure user-specific dashboards with real-time alerts, asset health indicators, and predictive insights. Integrate with existing APM or ERP systems for smooth workflows.
6. Testing, Optimization & Go-Live
Conduct pilot testing to validate predictions and system performance. Optimize algorithms based on results and scale the solution across the plant or multiple sites.
7. Continuous Monitoring & Improvement
Continuously refine AI models and update thresholds based on operational feedback. Add new asset types and enhance system intelligence with ongoing data collection.
Enhancing Overall Equipment Effectiveness (OEE) with Predictive Maintenance
Overall Equipment Effectiveness (OEE) is a critical metric for measuring how efficiently your equipment is utilized. Predictive maintenance powered by AI, IoT, and Agentic AI plays a vital role in improving OEE by reducing unplanned downtime, increasing asset availability, and optimizing performance.
Asset Performance Management (APM) for Predictive Maintenance Use Cases
FAQs
Predictive maintenance in APM refers to the use of AI and IoT technologies to anticipate equipment failures before they occur. It enables data-driven maintenance strategies that improve asset reliability and reduce unplanned downtime.
IoT plays a crucial role by collecting real-time data from sensors embedded in machines. This data is then analyzed by AI models within an APM platform to detect early signs of wear, anomalies, or failure.
APM is a strategic approach and set of tools that optimize asset health and efficiency. Using predictive maintenance powered by IoT and AI, APM improves operational visibility and extends asset life.
Agentic AI brings autonomous intelligence to predictive maintenance by enabling systems to not only predict issues but also initiate corrective actions-such as scheduling maintenance or adjusting operations-without human intervention.
An advanced APM solution includes IoT sensors for data collection, AI-powered analytics for condition monitoring, Agentic AI for autonomous actions, and dashboards for real-time asset performance tracking.
Predictive maintenance solutions combining AI and IoT can reduce maintenance costs by up to 30% and downtime by up to 50%, significantly enhancing APM outcomes.
Yes, modern APM platforms support integration with legacy equipment using IoT gateways and edge computing, enabling predictive maintenance without replacing entire infrastructure.
Industries such as manufacturing, oil and gas, utilities, mining, and transportation gain immense value from APM systems using IoT and Agentic AI to maintain equipment health and operational continuity.
Use cases include real-time motor vibration analysis in manufacturing, pipeline corrosion detection in oil & gas, transformer health monitoring in utilities, and fleet maintenance in logistics-all powered by IoT data and AI algorithms.
Predictive maintenance within APM helps organizations reduce unplanned outages, lower operational costs, increase safety, and boost Overall Equipment Effectiveness (OEE).
Agentic AI accelerates decision-making and automation in predictive maintenance, delivering faster responses, reduced labor costs, and maximized uptime-all contributing to higher ROI from APM investments.
By reducing unnecessary part replacements and optimizing energy usage, predictive maintenance with AI, IoT, and APM contributes to lower emissions and more sustainable operations.