Introduction
Overall Equipment Effectiveness (OEE) is a powerful metric in Asset Performance Management (APM) that helps organizations evaluate and optimize their manufacturing efficiency. By understanding how effectively production time is utilized, OEE provides a clear picture of equipment performance across three key factors: availability, performance, and quality. This comprehensive metric is invaluable for identifying improvement opportunities, reducing downtime, and implementing continuous improvement strategies like Lean Manufacturing and Six Sigma.
In addition to its role in performance evaluation, OEE also facilitates data-driven decision-making by providing actionable insights into operational inefficiencies. By continuously monitoring and analyzing OEE, organizations can pinpoint areas where equipment is underperforming, track maintenance needs, and make informed choices regarding asset management. This proactive approach not only helps maximize productivity but also extends the lifespan of assets, contributing to significant cost savings over time.
Why Overall Equipment Effectiveness (OEE) Matters in Manufacturing
For organizations focused on maximizing productivity, OEE serves as a benchmark to pinpoint inefficiencies and losses in the production process. By tracking OEE, companies can support initiatives aimed at minimizing downtime and defects, improving quality, and optimizing performance. As an industry standard, OEE also offers a clear, measurable way to track progress toward operational goals and is integral to the continuous improvement culture.
Calculating Overall Equipment Effectiveness (OEE)
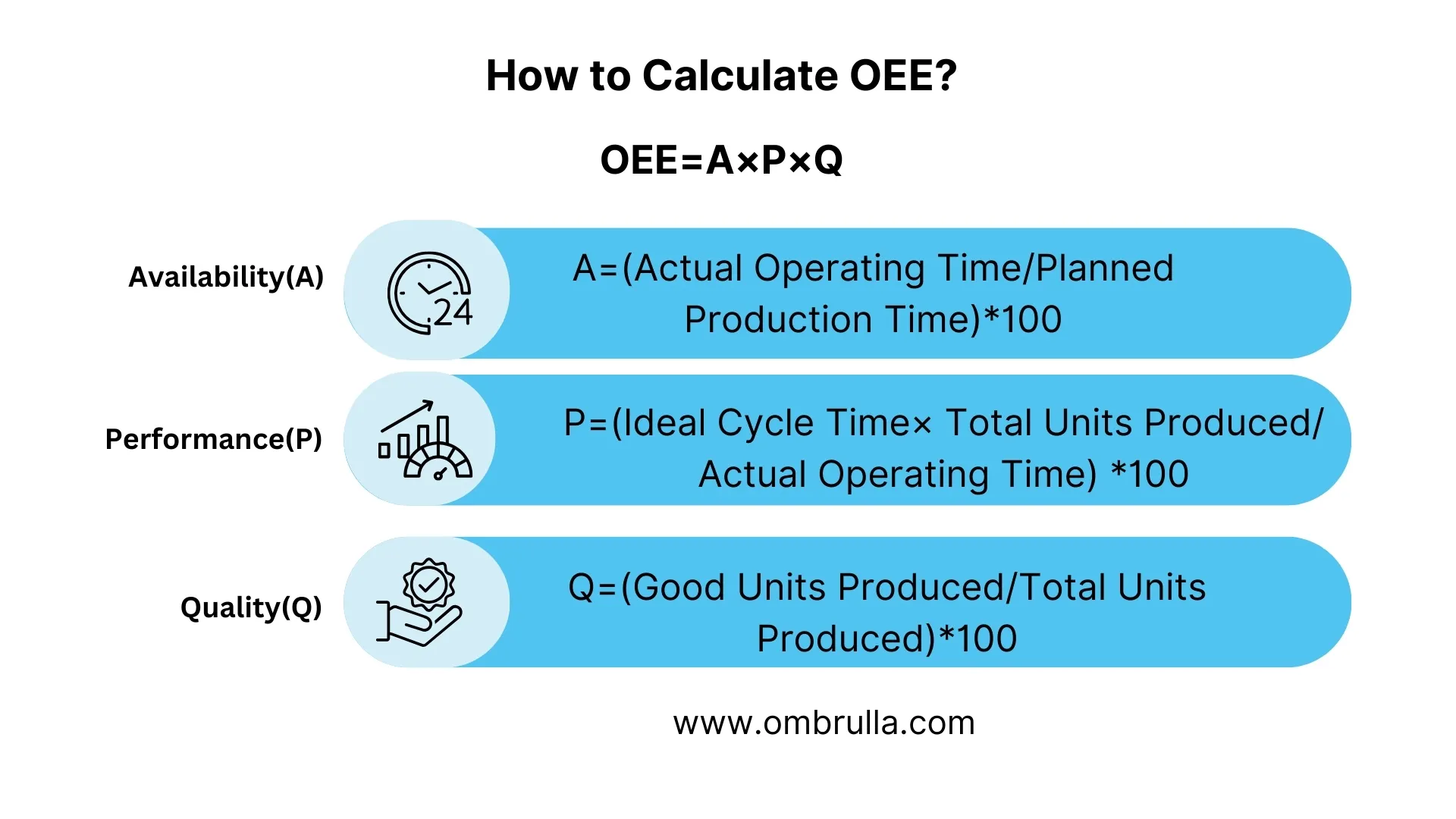
OEE is calculated by analyzing three primary components:
Availability:
Measures how often the equipment is ready for production.
Performance:
Tracks if equipment is running at its maximum speed.
Quality:
Evaluates the percentage of good parts produced compared to total parts.
“Efficiency is doing better what is already being done.”
-Peter Drucker
What is a Good OEE Score?
A perfect OEE score is 100%, indicating that production is running without any downtime, at optimal speed, and without defects. Although challenging to achieve, an OEE score of 85% or higher is considered world-class in discrete manufacturing. Scores between 60-84% suggest room for improvement, while scores below 60% highlight a need for significant operational changes.
Implementing OEE in Your Organization: Step-by-Step Guide
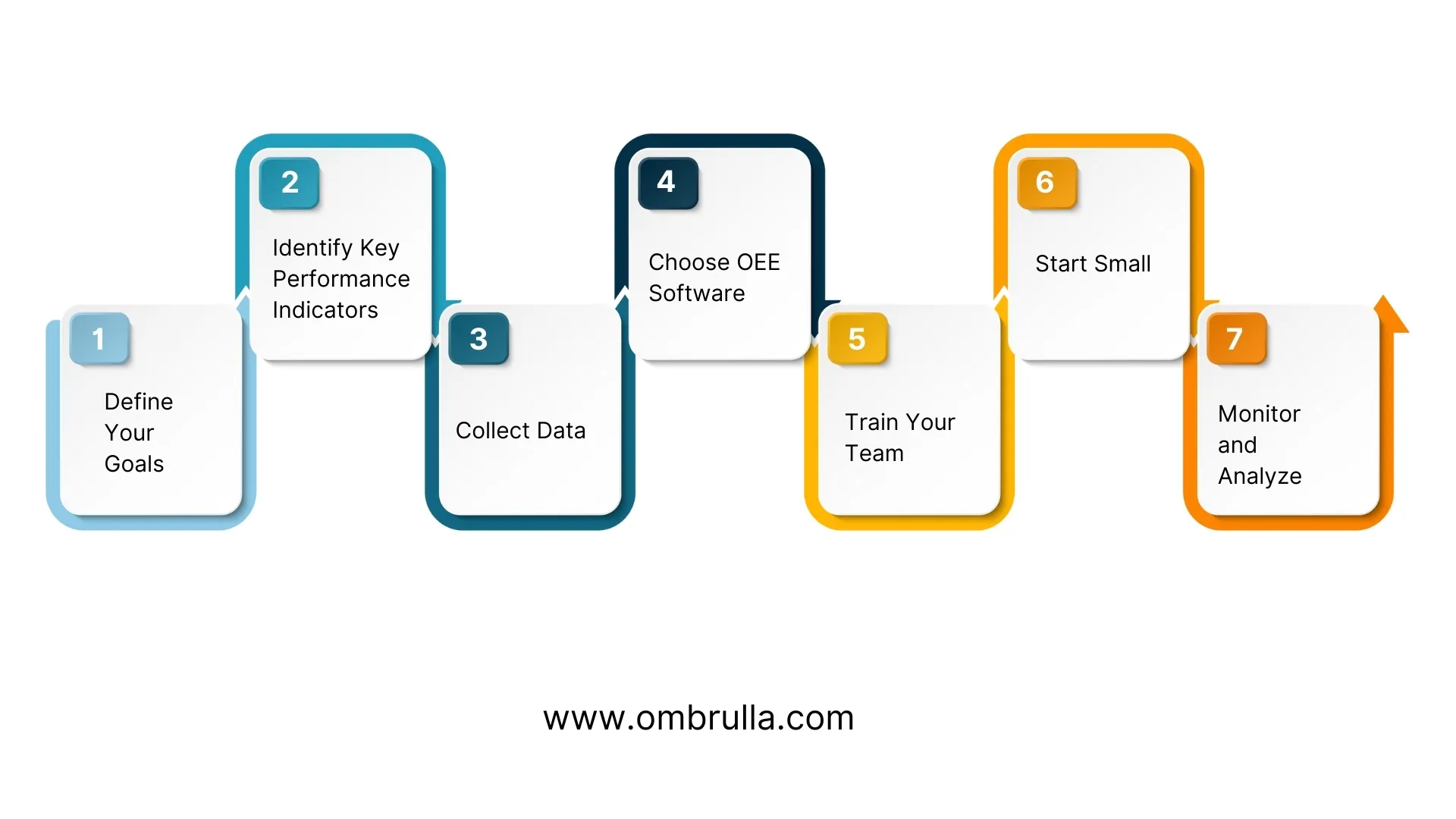
Successfully implementing OEE as part of your Asset Performance Management strategy requires a structured approach. Follow these steps to integrate OEE into your operations effectively:
Define Clear Goals
Start with a clear understanding of what you aim to achieve with OEE. Set specific, measurable objectives to reduce downtime, improve quality, or increase overall equipment effectiveness.
Identify Key Performance Indicators (KPIs)
Select KPIs that align with your organisational goals. Key metrics for OEE include Availability, Performance, Quality, and the overall OEE percentage.
Collect Accurate Data
Ensure data accuracy from reliable sources such as production logs, maintenance records, and quality control. IoT sensors and AI-enabled systems can capture real-time monitoring data for more accurate and actionable insights.
Choose OEE Software
Select OEE software that supports real-time tracking, data analysis, and report generation. Integrating with other systems like ERP, MES, and CMMS ensures seamless data flow and better asset performance management.
Train Your Team
Educate your team on OEE principles, data collection methods, and software use. Offer hands-on training and continuous learning opportunities to maintain alignment on OEE goals.
Start with a Pilot Project
Test the implementation process with a pilot project, gradually expanding as you refine the methodology.
Monitor, Analyze, and Improve
Regularly review OEE data to identify patterns and improvements. Use a data-driven approach to decision-making, driving continuous improvement in production efficiency.
How to Improve Overall Equipment Effectiveness (OEE)
Boosting OEE is an ongoing process that requires a focus on Availability, Performance, and Quality. By targeting these components with AI, IoT, and predictive maintenance, organisations can optimise production efficiency and reduce waste.
Increase Availability
To enhance availability, focus on minimizing equipment downtime with these techniques:
1. Preventive Maintenance:
Schedule regular maintenance to reduce unexpected breakdowns. Actions such as cleaning, inspecting, and replacing worn parts can prevent issues.
2. Predictive Maintenance Using AI and IoT:
Real-time monitoring with IoT sensors and AI-driven analytics can predict equipment failures before they occur, allowing for proactive repairs only when needed.
3. Quick Changeover Techniques (SMED):
Implement SMED methods to reduce setup times, such as separating tasks that can be done while machines are running and standardising setup tools.
4. Buffer or Parallel Machines:
For critical equipment, buffer stock or parallel machines can help maintain production during maintenance or repairs.
Enhance Performance
Improving performance involves optimising workflow, addressing inefficiencies, and empowering operators.
1. Optimize Workflow and Layout:
Conduct value stream mapping to eliminate bottlenecks and improve material flow. Reducing travel distances or arranging tools for quicker access can cut down on cycle times.
2. Address Setup Inefficiencies:
Minimize setup time by preparing tools, parts, and instructions beforehand.
3. Operator Training:
Well-trained operators are crucial for smooth equipment operation. Training on best practices, quick problem resolution, and performance monitoring is essential.
4. Real-Time Monitoring with IoT:
Use IoT sensors to monitor cycle times and other performance metrics. Immediate alerts when performance dips below benchmarks enable quick corrective action.
Boost Quality
Improving quality enhances OEE by reducing defects, rework, and scrap.
1. Identify and Correct Common Defects:
Use techniques like the Five Whys and Pareto Analysis to find root causes of frequent defects.
2. Standardise Procedures:
Consistent procedures reduce errors. Use SOPs, visual guides, and checklists for uniform production processes.
3. Statistical Process Control (SPC):
SPC methods detect when variations exceed acceptable limits, allowing for quick corrective action.
4. Automated Quality Checks:
Automation technologies, including machine vision, allow real-time, high-speed quality inspection, reducing reliance on manual checks and increasing accuracy.
Common Challenges in OEE Implementation
Implementing Overall Equipment Effectiveness (OEE) can transform manufacturing efficiency, but it presents several challenges. Here's an in-depth look at these common obstacles and their impact on OEE success:
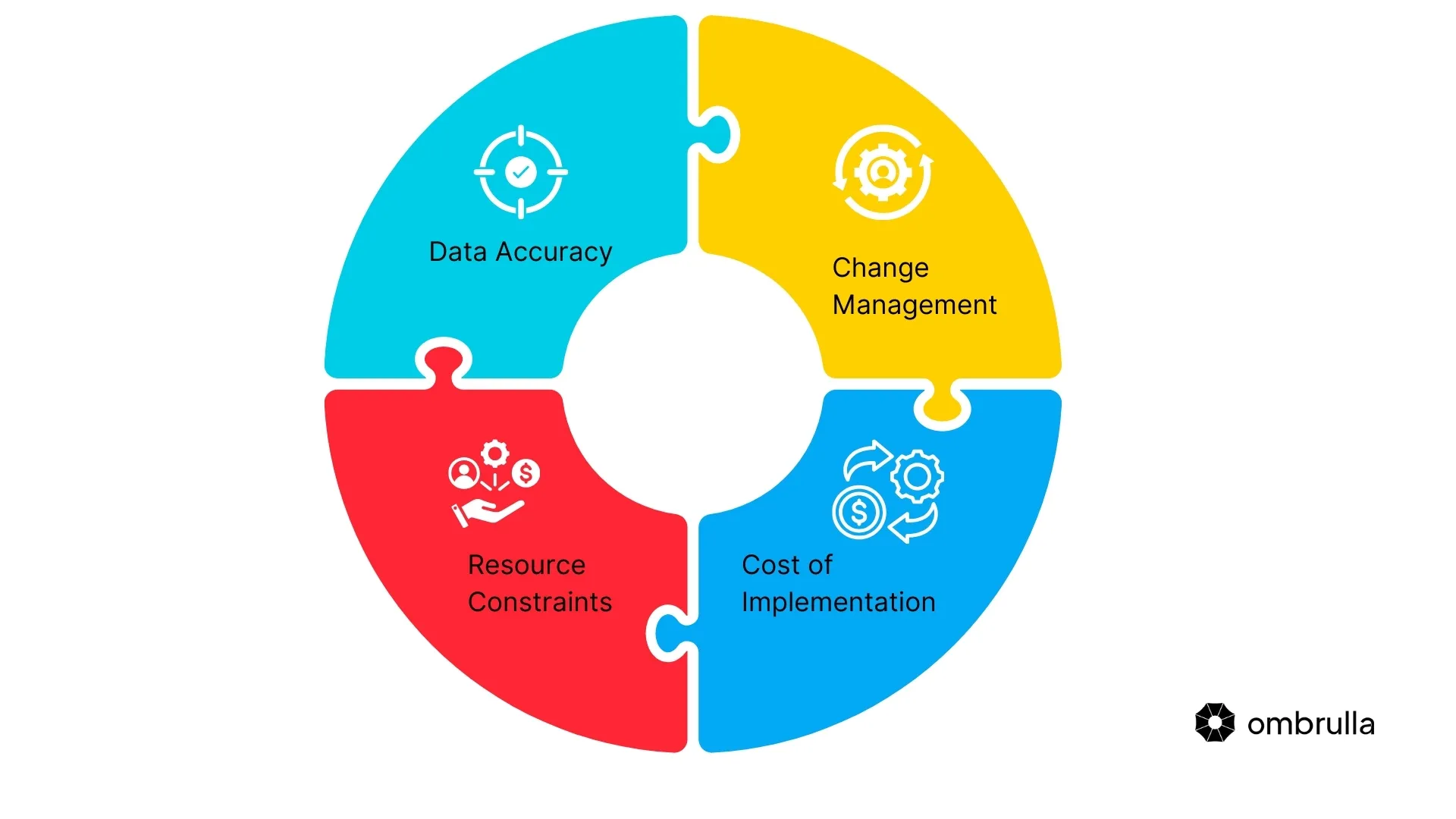
Data Accuracy
Accurate data is crucial for OEE, but it's often a challenge. Errors due to manual entry, sensor faults, or delayed logging can lead to inaccurate OEE calculations, which obscure inefficiencies and prevent proper root cause identification. Solutions include automating data collection, calibrating sensors regularly, and training operators on best data practices.
Resource Constraints
Small teams or facilities lacking advanced technology may struggle with the time, personnel, or tools needed for OEE. Constraints can delay corrective actions and allow inefficiencies to persist. To address this, companies can start with OEE tracking in high-impact areas and gradually expand as resources allow.
Change Management
Resistance to new processes, especially in established routines, can hinder OEE adoption. Employees may find OEE disruptive if they don't understand its value. Overcoming this challenge requires explaining OEE's benefits, involving employees in the process, and offering training to build familiarity.
Cost of Implementation
OEE implementation may involve expenses for software, sensors, or training, which can be prohibitive for smaller organisations. Starting with a phased approach, focusing on basic OEE tracking, and scaling as improvements are observed can help mitigate initial costs.
OEE to Drive Continuous Improvement
OEE can be leveraged to systematically identify inefficiencies, prioritise improvements, and track progress over time. Here's how:
1. Identify and Diagnose Inefficiencies
OEE breaks down efficiency into Availability, Performance, and Quality, making it easy to pinpoint issues:
Availability:
Downtime indicates the need for maintenance or changeover optimization.
Performance:
Slow cycles suggest workflow or training adjustments.
Quality:
High defect rates reveal areas for quality control enhancements.
2. Prioritise Improvement Efforts
OEE data highlights the most significant sources of inefficiency, helping teams focus on areas with the highest impact. For instance, if availability losses are the main issue, targeting uptime improvements will yield the greatest returns.
3. Support Lean Manufacturing and Six Sigma Initiatives
OEE aligns with Lean and Six Sigma, which aim to reduce waste and variability. It provides insights that support waste reduction, quality enhancement, and workflow optimization, allowing for a more focused application of Lean and Six Sigma principles.
4. Benchmark and Track Progress
Regular OEE tracking helps set benchmarks, monitor incremental improvements, and measure the impact of process changes over time, supporting long-term improvement strategies.
5. Foster a Culture of Continuous Improvement
OEE metrics can engage employees by quantifying their impact on production efficiency, fostering ownership and accountability across the team.
6. Use OEE Data for Root Cause Analysis
OEE data helps narrow down specific times and areas where inefficiencies occur, guiding teams to investigate factors like operator skill, equipment calibration, or production environment.
7. Implement Real-Time Monitoring for Immediate Improvements
Real-time OEE monitoring enables quick responses to inefficiencies, reducing downtime and ensuring faster corrective action.
8. Optimise Continuous Improvement Cycles
OEE facilitates continuous improvement by providing a cycle of feedback. Teams can refine their strategies over time, ensuring each improvement cycle builds on previous lessons.
Limitations of OEE
OEE is a valuable metric, but it has limitations:
Focus on Equipment
OEE primarily assesses equipment, potentially overlooking labor, material quality, and process factors that also impact production.
Data Accuracy
Accurate data is difficult to maintain, particularly with manual entry or unreliable sensors. Ensuring consistent accuracy can be costly and resource-intensive.
Complexity in Implementation and Maintenance
Implementing OEE in large or multi-site environments requires resource dedication, integration with existing systems, and consistency across varied machinery.
“What gets measured gets managed. If you can't measure it, you can't improve it. It is essential to have a clear understanding of what metrics drive performance in order to make informed decisions and achieve lasting improvements.”
-Peter Drucker
OEE to Optimise Production Scheduling
OEE data supports more effective production scheduling, allowing organisations to align production activities with equipment capabilities, minimise downtime, and increase throughput.
Identify Bottlenecks and Constraints
OEE highlights underperforming equipment and bottlenecks in availability, performance, and quality, helping managers prioritise maintenance and workflow adjustments.
Optimise Production Schedules with Realistic Capacity Planning
By aligning production schedules with actual availability, performance, and quality metrics, OEE enables realistic capacity planning and reduces production disruptions.
Improve Load Balancing for Maximum Utilisation
OEE data supports workload distribution across equipment, preventing overuse of certain machines and balancing workload to maximise equipment lifespan and reduce downtime.
Integrate OEE with Other Performance Metrics
Integrating Overall Equipment Effectiveness (OEE) with other Key Performance Indicators (KPIs) offers a comprehensive view of operational performance, aiding organisations in optimising resources and improving productivity.
Combining OEE with Key KPIs:
Throughput:
Measures production rate. Analyzing it with OEE can identify bottlenecks; high OEE but low throughput signals potential production flow issues.
Cycle Time:
Tracks time per production unit. Paired with OEE, it reveals discrepancies between expected and actual speeds. Short cycle time with high OEE indicates efficiency, while long times suggest downtime or suboptimal performance.
Production Costs:
Integrating cost metrics with OEE highlights financial inefficiencies. Metrics like maintenance, labour, and energy costs correlated with OEE scores provide insights into cost per unit. High OEE with low costs indicates efficiency; high costs suggest areas for cost optimization.
Applying OEE in Service Operations:
Service Availability:
Reflects uptime of resources (e.g., call center agents, medical equipment). Monitoring helps identify accessibility issues, such as staffing shortages or system downtimes.
Service Performance:
Assesses service speed, like call duration or patient exam times. Low performance scores suggest the need for process improvement or additional resources.
Service Quality:
Tracks errors and customer satisfaction (e.g., call resolution rates, patient feedback). High Quality scores reflect effective service delivery; low scores highlight areas needing improvement.
Adapting OEE for service industries helps enhance resource management and customer satisfaction, boosting overall efficiency.
Conclusion
Overall Equipment Effectiveness (OEE) is a key metric for optimizing production by measuring availability, performance, and quality. Integrating OEE with KPIs like throughput and cycle time provides a holistic view, helping identify inefficiencies and improve productivity. A strategic OEE approach drives efficiency, cost optimization, and sustainable growth while maintaining a competitive edge.




Related Blogs



