Introduction
AI Visual Inspection is redefining quality control in today’s competitive manufacturing landscape. By replacing time-consuming, error-prone manual inspections with intelligent, automated systems powered by computer vision and deep learning, this technology ensures consistent, objective, and highly accurate defect detection. In this blog post, we explore how AI Quality Control is transforming manufacturing operations, boosting efficiency, reducing waste, and setting new benchmarks for product excellence.
What is AI Visual Inspection?
AI Visual Inspection refers to the use of artificial intelligence, specifically computer vision, to assess the quality of products through image recognition and analysis. Unlike traditional manual inspection, AI systems can identify defects, irregularities, and inconsistencies in real time, providing accurate results faster and more reliably.
1. AI Quality Control:
With AI, you can enhance your quality control processes by automating defect detection, ensuring better accuracy in product evaluation.
2. AI Defect Detection:
Using advanced algorithms, AI Defect Detection systems can identify even the smallest flaws such as scratches, discolorations, or misalignments that are often missed in manual inspection.
3. Computer Vision
AI Visual Inspection relies on computer vision, a field that enables machines to interpret and understand visual data, much like humans do with their eyes.
The Limitations of Manual Inspection
Manual inspection has long been the cornerstone of quality control. Human inspectors meticulously examine products for defects, relying on their eyesight and judgment. While effective to some extent, this approach suffers from several inherent limitations:
1. Subjectivity
Human judgment can vary between inspectors, leading to inconsistent results. Fatigue, distractions, and personal biases can all influence an inspector's assessment.
2. Inconsistency
Even the most experienced inspectors can miss subtle defects, especially in high-volume production environments. Consistency is difficult to maintain over extended periods
3. Slow Speed
Manual inspection is inherently slow, especially for complex products or large production runs. This can create bottlenecks and delay production.
4. High Cost
Employing and training a team of skilled inspectors can be expensive. Furthermore, the costs associated with rejected products and rework can be substantial.
5. Limited Data Insights
Manual inspection often generates limited data, making it difficult to identify trends and proactively address quality issues.
These limitations highlight the need for a more robust and efficient approach to quality control. This is where AI Visual Inspection steps in.
Step-by-step process of AI Visual Inspection
AI Visual Inspection offers a powerful alternative to traditional methods. It leverages computer vision, a field of artificial intelligence that enables computers to see and interpret images and videos, to automate the detection of defects. Here's how it works:
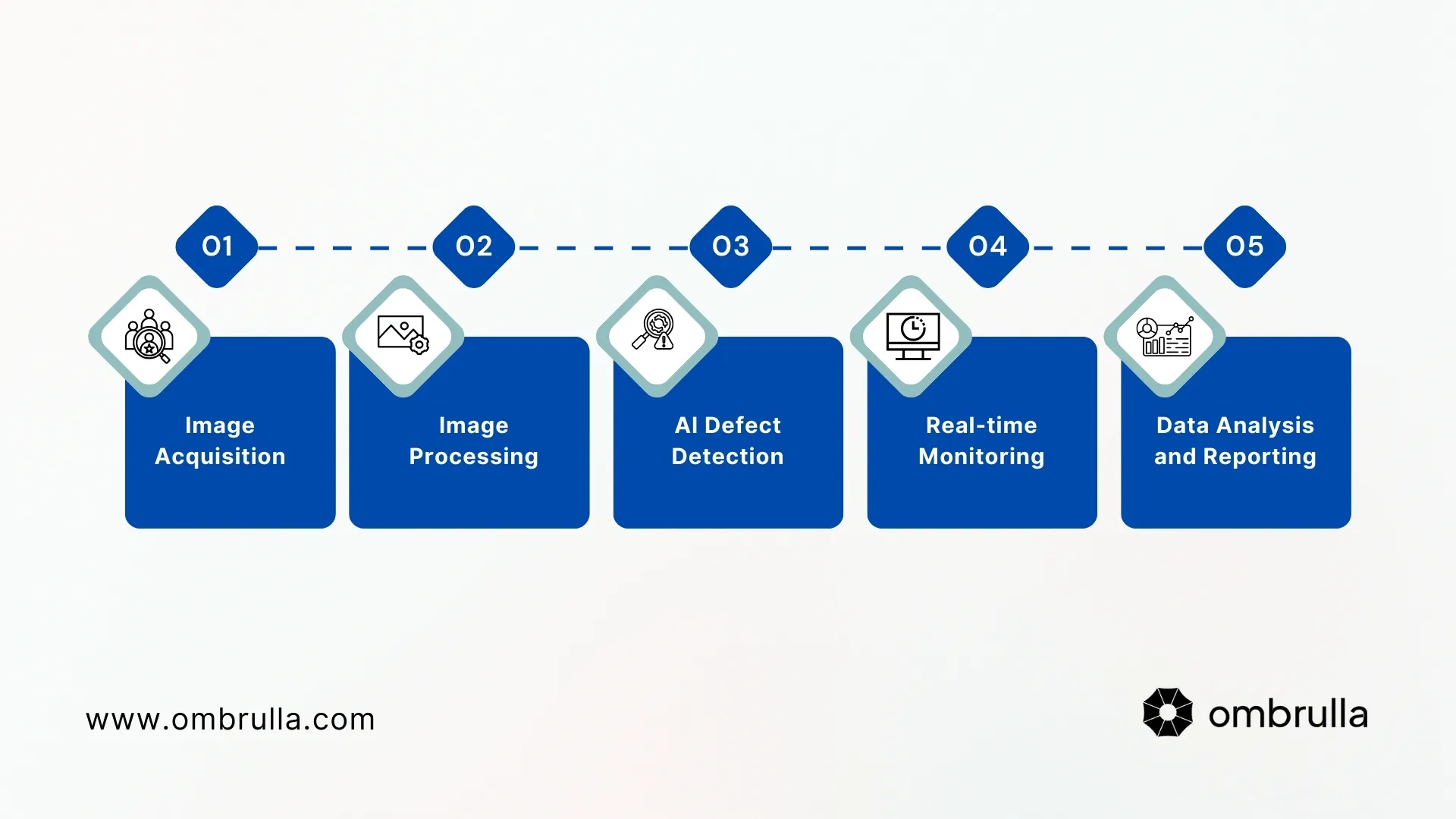
1. Image Acquisition
High-resolution cameras capture images of products at various stages of the manufacturing process.
2. Image Processing
The captured images are pre-processed to enhance their quality and prepare them for analysis.
3. AI Defect Detection
A pre-trained AI model, typically a deep learning neural network, analyzes the images to identify anomalies and defects. The model has been trained on a vast dataset of images, learning to recognize both acceptable and unacceptable variations.
4. Real-time Monitoring
The AI system, equipped with Real-time Monitoring, can continuously observe the production line and provide immediate feedback on product quality, ensuring defects are detected and addressed without delay.
5. Data Analysis and Reporting
The system generates detailed reports on defect types, frequency, and location, providing valuable insights for process improvement.
Benefits of AI Quality Control
Implementing AI Quality Control offers a multitude of benefits:
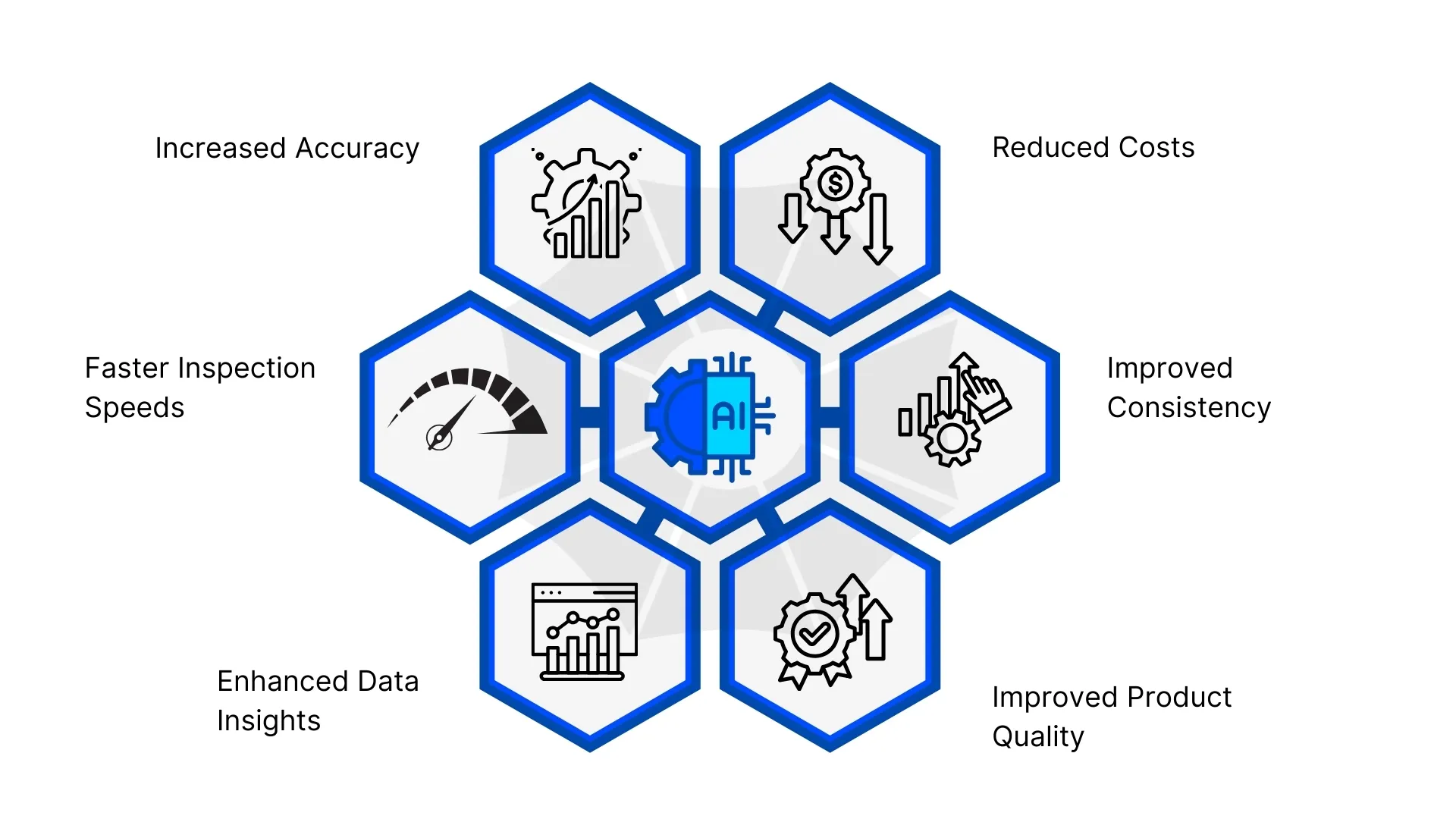
1. Increased Accuracy
AI-powered systems can detect even the most subtle defects with a higher degree of accuracy than human inspectors. This reduces the risk of faulty products reaching customers.
2. Improved Consistency
AI systems provide consistent and objective assessments, eliminating the variability associated with manual inspection.
3. Faster Inspection Speeds
AI Visual Inspection can significantly speed up the inspection process, enabling faster production cycles and increased throughput.
4. Reduced Costs
By automating inspection and reducing the number of rejected products, AI can lead to significant cost savings.
5. Enhanced Data Insights
AI systems generate rich data that can be used to identify trends, optimize production processes, and prevent future defects.
6. Improved Product Quality
Ultimately, AI Quality Control leads to higher product quality, enhancing customer satisfaction and brand reputation.
Case Study: Enhancing Safety for Lone Workers with Advanced Monitoring Solution
Case Study 1: Steel Rail Inspection with AI Visual Inspection
Problem:
Manual inspection was slow, inconsistent, and prone to errors, leading to defective rails reaching customers.Solution:
An AI Visual Inspection system was implemented for real-time analysis of surface and internal defects.Results:
Increased accuracy, enhanced speed, cost efficiency, scalability, data-driven insights, and improved customer satisfaction.
Case Study 2: Fabric Inspection in Textiles with AI Visual Inspection
Problem:
Manual inspection suffered from variability, high labor costs, slow speeds, undetected imperfections, and scalability issues.Solution:
An AI Visual Inspection system was integrated to detect tears, stains, and pattern irregularities.Results:
Increased accuracy, enhanced efficiency, cost savings, scalability, data-driven insights, and improved customer satisfaction.
Case Study 3: Automotive Paint Inspection with AI Visual Inspection
Problem:
Manual inspection led to inconsistencies, high labor costs, slow processes, inaccurate defect detection, and scalability challenges.Solution:
An AI Visual Inspection system was implemented to identify imperfections in paint finishes.Results:
Improved defect detection accuracy, enhanced operational efficiency, cost efficiency, scalability and consistency, actionable insights, and improved customer satisfaction. This highlights the value of AI visual inspection in the automotive industry for achieving superior paint quality.
These case studies demonstrate the tangible benefits of AI Visual Inspection across diverse manufacturing sectors. The consistent themes are improved accuracy, speed, cost-effectiveness, and data-driven insights, all contributing to higher quality products and greater customer satisfaction.
The Future of Visual Quality Control
Visual Quality Control is rapidly evolving, driven by advancements in AI and computer vision. We can expect to see even more sophisticated AI models capable of detecting increasingly complex defects. Real-time monitoring will become even more prevalent, enabling manufacturers to proactively address quality issues before they escalate. The integration of AI with other technologies, such as robotics and automation, will further transform the manufacturing landscape.
Conclusion
AI Visual Inspection is revolutionizing manufacturing inspection by providing a more accurate, consistent, and efficient approach to quality control. By embracing AI Quality Control, manufacturers can significantly improve product quality, reduce costs, and enhance their competitiveness. As AI technology continues to advance, we can expect to see even greater adoption of AI Defect Detection in the years to come. This represents a significant shift from traditional manual inspection practices, paving the way for a future of smarter, more efficient manufacturing. The benefits of Quality Visual Inspection are undeniable, and businesses that fail to adopt this technology risk falling behind.




Related Blogs



